With the rapid development of the new energy industry, manufacturing technologies for battery components are receiving increasing attention. Ultrasonic welding, as an efficient, clean, and reliable bonding technology, has become a key process in battery manufacturing. Below is an analysis of its main applications and advantages.
1. Working Principle of Ultrasonic Welding
Ultrasonic welding uses high-frequency mechanical vibrations to generate localized frictional heat at the surface of the materials being welded, enabling the bonding of their molecules. The process consists of the following steps:
StepDescription1. ContactThe welding tool comes into contact with the materials and applies pressure.2. VibrationHigh-frequency vibrations generate frictional heat between the materials.3. MeltingThe contact surfaces melt locally.4. SolidificationAfter the vibrations stop, the materials cool down and form a strong bond.
2. Application Scenarios and Examples
Ultrasonic welding is widely used in battery components. Specific scenarios and their advantages are summarized in the table below:
Application ScenarioIllustrationAdvantagesTab-to-busbar weldingHigh material compatibility and excellent conductivity.Battery casing sealingLeak-proof, high precision, and improved safety.Multi-layer material weldingHigh efficiency, suitable for mass production.Wire harness to terminal connectionHigh strength, low resistance, and reduced energy loss.
3. Comparison of Ultrasonic Welding and Traditional Welding
The table below highlights the advantages of ultrasonic welding compared to traditional welding:
Comparison ItemUltrasonic WeldingTraditional WeldingTemperature ControlLow temperature, prevents material damageHigh temperature, may damage materialsEnvironmental FriendlinessNo solder or chemical agents requiredMay produce pollutantsApplicabilitySuitable for metals, plastics, and compositesRequires specific materialsAutomation CapabilityEasy to automateDifficult to automate
4. Future Prospects
The following chart illustrates the growth trend of ultrasonic welding in the new energy battery manufacturing market (data sourced from industry research reports):
Expected Growth by 2025: Market size will reach $20 billion.
Key Drivers: Rapid demand growth in electric vehicles and energy storage systems.
The widespread application of ultrasonic welding in battery components not only improves production efficiency but also provides reliable technical support for green manufacturing. With continuous technological innovation, its importance in the new energy industry will become even more prominent.
https://mechtechsupply.com/pro....duct-category/ultras
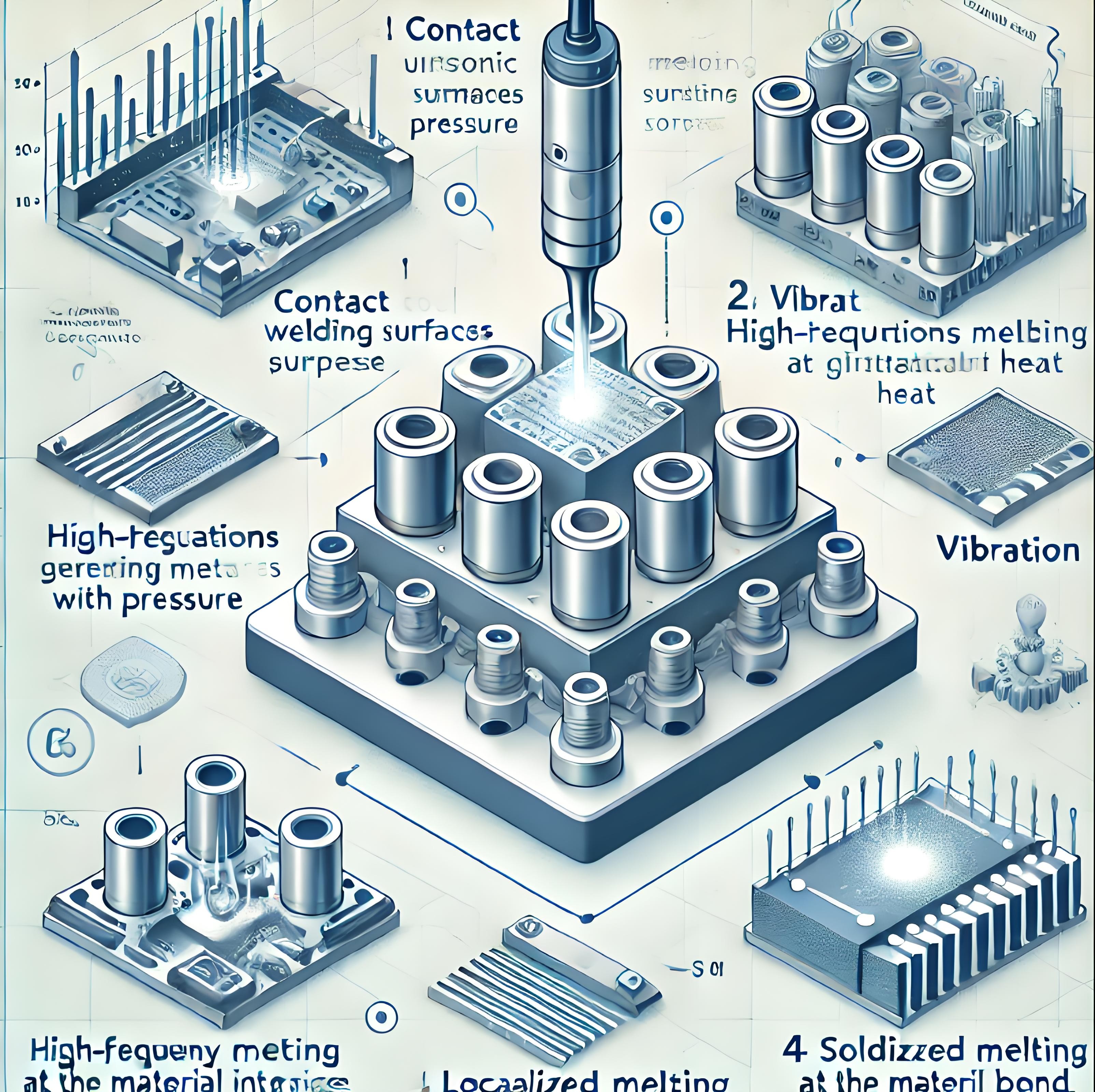